Definition: it is the process of arranging, controlling and optimizing work and workloads in a food production process or manufacturing process. Scheduling is used to allocate plant and machinery resources, plan human resources, plan production process and purchase materials.
Production and manufacturing run on timelines. You receive orders, sometimes concurrently, and you plan the steps in your manufacturing schedule to ensure parts of the process are completed in proper sequence as efficiently as possible. Creating an effective and efficient production schedule can cut payroll costs and keep frustration to a minimum.
Function/purpose of production scheduling:
- To maintain the production time and costs
- To maximize the efficiency of the operation and reduce cost.
Production scheduling can involve random attributes, such as random processing times, random due dates, and random weights etc.
Key concepts in production scheduling:
- Inputs: inputs are plant, labour, materials, tooling, energy and a clean environment.
- Output: these are the products produces in food production department.
- Output for other kitchen department: the output of any kitchen within the hotel is an input to the next kitchen according to the preparation of dishes such as: the main kitchen is responsible for many activities or pre-preparations which are sent to the particular concerned department. Larder kitchen is responsible for cutting of desired meat cuts and supply to the various kitchen.
- Output within the kitchen department: each and every food production department to do its own mis-en-place and to produce the final food products.
- Output for the customer: the kitchen output (final products) are served to the customer via a service.
- Resource allocation: it is assigning inputs to produce output. The aim is to maximize output with given inputs.
The importance of production scheduling:
- to avoid the customer’s frustration with prompt services
- to prevent chef’s stress by motivating them
- using various methods to find ways to optimize the production flow
- try to make no mistake while preparations.
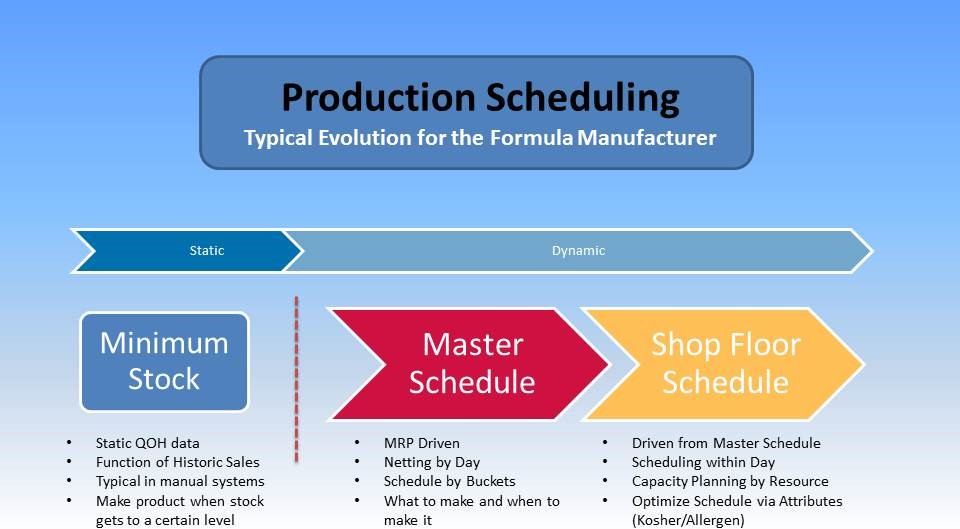
4 Components of Production Scheduling
The four components of production scheduling include the following:
- Planning – The planning component of production scheduling is by far the most important. The planning component pertains to deciding in advance what should be done in the future – which is the most crucial step in production scheduling. Without a plan, production scheduling can not even begin or take place. Preparing a plan through charts, production budgets, or various others visual representations can provide a sound basis for steps down the road pertaining to production.
- Routing – Production routing is the process that pertains to determining the route or path that a product must follow. This route entails the path from raw materials until it transform into a finished product. The main objective of this component is to locate and perform the most economical and enhanced sequence of operations in the production process.
- Scheduling – Scheduling coincides with the time and date that the operation must be completed. Scheduling is an essential and crucial portion of production scheduling and lays the foundation and groundwork for all of the steps within the production process. There are three types of scheduling that an operations utilize, such as master scheduling, manufacturing or operation scheduling, and retail operation scheduling. Overall, scheduling is key for a manufacturing operation to proceed.
- Dispatching – Dispatching relates to the process of initiating production with a preconceived production plan. Dispatching is concerned with giving a practical shape to an overall production plan. This will also include issuing any orders and instructions and other important information pertaining to production.
Advanced planning and scheduling software (APS) utilizes the four components of production scheduling and can provide thorough insight within your manufacturing operation.
Advanced Planning and Scheduling (APS)
Advanced Planning and Scheduling (APS) software has become a must for modern-day manufacturing operations due to customer demand for increased product mix and fast delivery combined with downward cost pressures. APS can be quickly integrated with a ERP/MRP software to fill gaps where these system lack planning and scheduling flexibility and accuracy. Advanced Planning and Scheduling (APS) helps planners save time while providing greater agility in updating ever-changing priorities, production schedules, and inventory plans.
- Create optimized schedules balancing production efficiency and delivery performance
- Maximize output on bottleneck resources to increase revenue
- Synchronize supply with demand to reduce inventories
- Provide company-wide visibility to capacity
- Enable scenario data-driven decision making
Implementation of Advanced Planning and Scheduling (APS) software will take your manufacturing operations to the next level of production efficiency, taking advantage of the operational data you already have in your ERP.